This is Peter brazing a lugged Muldyr of Reynolds 931...
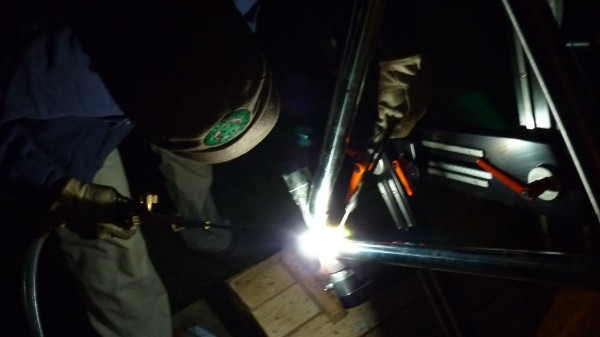
We, Christian and Peter, build steel frames. Trekking and touring bikes, cyclocrossbikes, roadbikes, mountainbikes, fatbikes and even dogscooters if you would ask politely enough. We do have some experience with different tubesets from pigshed-iron to space-steel if you like and we work together with a braze supplier to test different kinds of materials. We have some experience with almost all known tube suppliers. We like the brazing process. It still is the most versatile way to link tubes we think. Depending on what you like. More comfy or more rigid. Braze, silver, lugs or fillet.
If you are interested in the process of brazing a bike and if you fancy a true diehard bike that will neither cost a fortune nor look and behave as a princess, if you fancy a handmade worker with a sturdy and real look you might have come to the right place.
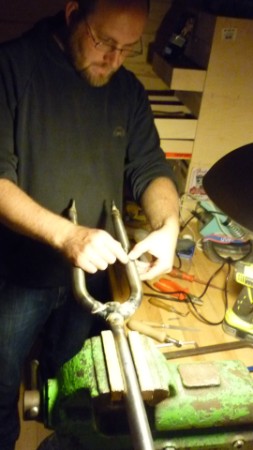
Our frameshop, "The Cyclery", is the place our frames come from. We do all the metalworks in house. Just for the powdercoating we ask a local shop. We are conscious about the process beeing local and environment-friendly. That's beneath the "real-steel-feel-factor" and the still impressive performance and longevity one more reason to stay with steel as frame material.
The idea to start our own frame building shop came when more and more of our bikebuilding icons disappeared or joined with some mass manufactorers. The remaining were financially out of reach for us and finally we wanted still bikes not pieces of art. Sturdy steel bikes designed and built by people who just love the ride who care about the building process, the performance and the footprint of the whole idea.
...and Christian assembling a Reynolds 631 lugged fork for a Muldyr.